In Canada, Good Manufacturing Practices (GMP) for Natural Health Products (NHPs) are essential guidelines that ensure products are manufactured safely, consistently, and in line with high quality standards. These practices cover every step of the product lifecycle, from sourcing raw materials to the final packaged product.
This blog will explore the key aspects of GMP compliance, including the role of the Quality Assurance Person (QAP), the importance of supplier controls, sanitation protocols, and the critical processes for validating manufacturing and preventing contamination. We will also discuss how these standards contribute to the safety of NHPs, and how manufacturers can meet Health Canada’s regulatory requirements while fostering consumer trust and confidence. Understanding and implementing these practices is not only vital for compliance but also for ensuring the quality and safety of products in the NHP market.
What are GMPs for NHPs?
In Canada, Good Manufacturing Practices (GMPs) for Natural Health Products (NHPs) are regulations set by Health Canada to ensure that products such as herbal supplements, vitamins, and homeopathic medicines are manufactured safely, consistently, and in compliance with high-quality standards. These guidelines are designed to minimize risks to consumers by ensuring that NHPs are produced in controlled environments, which prevent contamination, while maintaining product integrity throughout the lifecycle of an NHP.
To comply with these standards, all Canadian manufacturers, packagers, labellers, and importers of NHPs must obtain a valid site licence from Health Canada. This licence confirms that the company adheres to GMP regulations and has proper quality control and assurance systems in place. Additionally, manufacturers are required to keep thorough records of production processes, raw material documentation for traceability, and testing results to demonstrate compliance with GMP guidelines.
Another essential aspect of GMPs is sanitation. Strict protocols must be followed to prevent contamination during production, packaging, and storage. GMP regulations also govern the storage and distribution of NHPs to ensure that these products remain safe, effective, and maintain their integrity throughout their shelf life. Whether the product is made in Canada or abroad, manufacturers and importers are required to ensure that the product remains in proper condition until it reaches the consumer.
Quality Assurance Person (QAP) in the GMP Context
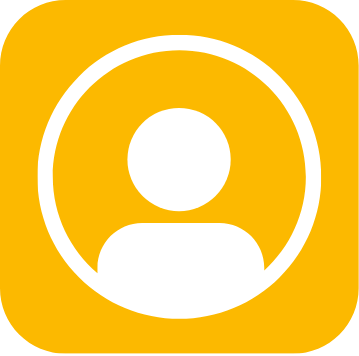
A key element of GMPs for NHPs is the mandatory appointment of a Quality Assurance Person (QAP) at each licensed site. The QAP oversees the production process, ensuring that products meet safety, quality, and regulatory standards. Their primary responsibility is verifying that the final product certificate of analysis aligns with the relevant monograph, finished product specifications and all other regulatory requirements before the product is released to the market.
For both domestic and imported NHPs, GMP compliance is required. Importers are responsible for ensuring foreign manufacturers follow GMP guidelines and meet regulatory standards. They appoint their own QAP to review testing documentation for each lot before shipment to Canada. NHPs can only be released to the Canadian market once the importer reviews the documentation and confirms compliance with Canadian standards.
The QAP must have comprehensive NHP knowledge, including an understanding of GMP principles and their application in the industry. They are responsible for creating and updating Standard Operating Procedures (SOPs), conducting internal GMP audits, and addressing quality concerns through corrective actions.
The QAP also reviews product specifications, batch records, and certificates of analysis to ensure compliance with regulations. They evaluate raw material specifications, interpret test results, and implement risk management strategies. Additionally, the QAP manages pest control, ensures adherence to chemical safety guidelines (e.g., WHMIS), and oversees product recalls should they occur. Their knowledge extends to stability studies and all stages of NHP manufacturing, packaging, and labelling to ensure product quality and safety.
Why GMP Matters for NHPs?
Good Manufacturing Practices (GMP) are essential for ensuring that NHPs are safe, effective, and consistently of high quality. By setting clear standards, GMPs help guarantee that each product is made to specific, tested specifications, so that consumers get a reliable product every time.
One of the most important reasons GMPs matter is because they ensure consistency. Each lot of NHPs is manufactured to the same standards, so consumers can trust that the product will perform as expected every time they purchase. Without GMPs, the quality or potency of the product could vary, leading to potential safety issues, adverse reactions, or making the product less effective.
GMPs also focus on preventing contamination throughout the manufacturing process. Strict sanitation protocols help ensure that the product remains free from harmful substances, such as bacteria, heavy metals, or other contaminants that could compromise its safety and integrity. This is especially critical for NHPs, where the purity of ingredients is vital.
Additionally, GMPs cover the entire product lifecycle, from the sourcing of raw materials to the final distribution. This means that every step of the process is regulated, ensuring that all ingredients are tested for quality and the final product is in optimal condition before it reaches the consumer.
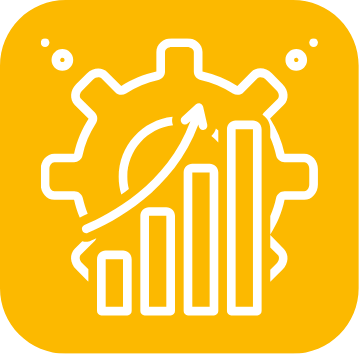
Finally, GMPs help build consumer trust. When a product is manufactured under GMP standards, consumers can feel confident that it meets high safety and quality standards. In a market filled with countless health products, knowing that a product is made according to GMP guidelines offers peace of mind that it is safe, effective, and reliable.
GMP Requirements for Natural Health Products in Canada
Good Manufacturing Practices (GMP) consist of a comprehensive set of requirements designed to ensure that Natural Health Products (NHPs) meet high standards of quality, safety, and consistency when produced. The following section highlights the key elements of GMP compliance specific to NHPs.
Compliance with the Canadian NHP Regulations
Under the Natural Health Products Regulations, all manufacturers, packagers, labellers, and importers of NHPs must hold a valid Site Licence, as outlined in Section 27. This licence confirms that the site complies with GMP requirements.
Although distributors and storage facilities must follow GMP practices, they are not required to be licensed. However, they are still expected to implement and adhere to quality controls consistent with Health Canada’s standards and have an appointed QAP. For example, a third-party warehouse storing NHPs must maintain appropriate temperature and humidity controls, ensure products are stored securely and segregated by lot. Additionally, they must have written procedures for inventory management and handling damaged goods, despite not requiring a site licence.
Establishing a Quality System
A robust quality system is essential for GMP compliance. This system should include quality assurance (QA) and quality control (QC) components. QA ensures consistent manufacturing processes through documented procedures, systematic sampling, and final product release protocols. QC involves testing materials and products to verify they meet established specifications.
Raw Material and Supplier Controls
To reduce the risk of contamination—one of the most common reasons for NHP recalls—manufacturers must establish rigorous supplier qualification procedures. All raw materials must be tested for identity, purity, and potency, and only materials that meet established specifications should be used in production. Each ingredient must be tested in accordance with applicable monographs and recognized pharmacopoeial standards, such as those outlined in the U.S. Pharmacopoeia (USP) or European Pharmacopoeia (Ph. Eur.), unless specifically exempted by Health Canada.
For example, if a manufacturer is using ashwagandha (Withania somnifera) root in an NHP, the raw material must be tested to confirm its botanical identity—often through high-performance thin-layer chromatography (HPTLC)—and verified for active constituents such as withanolides, as specified in pharmacopoeial standards. Only batches of raw material that meet these requirements should be approved for use in the final NHP formulation.
Manufacturing Process Controls
Manufacturing must follow validated processes to ensure consistency and product quality. This includes maintaining clean facilities, calibrated equipment, proper employee hygiene, and controlled environmental conditions. Adhering to these protocols helps reduce variability and the potential for contamination.
Record-Keeping Requirements
Accurate documentation is a key GMP requirement. All production, testing, and distribution records must be maintained for at least one year after the product’s expiration date. Both physical and electronic records, including those with e-signatures, are acceptable, provided they are audit-ready and comply with data integrity standards.
Internal Audits and Ongoing Compliance
Regular internal audits are essential for verifying continuous compliance with GMP requirements. Whether manufacturing occurs domestically or abroad, the Canadian site licence holder is ultimately responsible for ensuring that all activities such as production, packaging, labelling, and testing meet Health Canada’s regulatory standards.
For imported products, this includes verifying that foreign sites follow equivalent GMP protocols. Site licence holders must maintain documented evidence of compliance, such as audit reports, quality technical agreements, and batch documentation, to demonstrate oversight and ensure product quality throughout the supply chain.
For example, if a Canadian company is importing capsules containing ashwagandha root extract from a manufacturer outside of Canada, the site licence holder must ensure that the foreign facility has been audited for Canadian GMP compliance appropriate for NHPs, that each batch includes validated testing results for identity and withanolide content, and that the product meets specifications before it can be released for sale.
Product Testing and Stability
Finished products must undergo testing to confirm they meet quality specifications before release to the market for consumer consumption. In addition, stability testing is required to verify that a product maintains its quality, safety, and efficacy throughout its shelf life, supporting label claims and consumer confidence.
Complaint Handling and Recall Management
Manufacturers and distributors must have procedures in place to manage complaints and execute product recalls if necessary. In the event of a recall, Health Canada must be notified within three calendar days. An effective complaint and recall system is critical for protecting public health and maintaining regulatory compliance.
For example, if a batch of ashwagandha capsules is found to be contaminated with an unapproved ingredient, the manufacturer must immediately initiate a recall process. This includes notifying Health Canada within three days, informing customers and distributors of the recall, and retrieving affected products from the market. The manufacturer must also investigate the root cause of the contamination and implement corrective actions to prevent recurrence, all while keeping detailed records of the entire process for regulatory review.
Key Principles of NHP GMPs
Key GMP principles include maintaining hygiene and sanitation, validating manufacturing processes, preventing cross-contamination, and ensuring proper labelling and packaging. Adhering to these practices helps reduce risks, ensures product consistency, and protects public health.
Maintain Hygiene and Sanitation
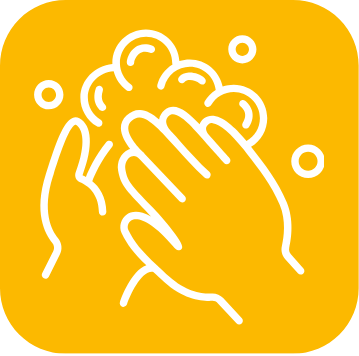
Hygiene and sanitation are fundamental to GMP compliance. Manufacturing facilities must adhere to strict cleaning protocols to prevent cross-contamination. Water used in production must be potable and comply with Canadian Drinking Water Guidelines or equivalent standards such as those set by the World Health Organization (WHO).
Equipment and surfaces in direct contact with NHPs should be regularly cleaned, maintained, and inspected to ensure they are free from residues. Additionally, staff must undergo training on personal hygiene and sanitation practices to minimize contamination risks.
Validate Manufacturing Processes
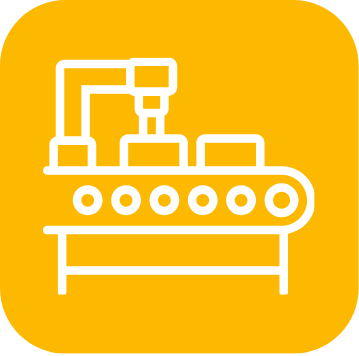
Manufacturing processes must be validated to ensure they consistently produce products that meet defined specifications. This involves comprehensive testing, detailed documentation, and close monitoring of production practices.
For instance, temperature-sensitive ingredients like ashwagandha extracts must be processed within specified temperature ranges to maintain their potency. Validation also includes equipment calibration and operational qualification to ensure that each manufacturing step complies with regulatory standards.
Prevent Cross-Contamination
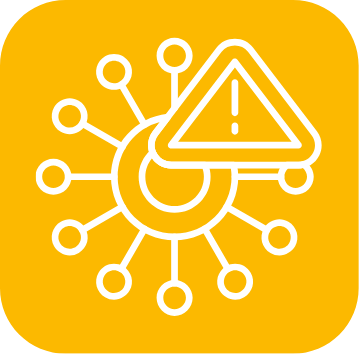
Facilities must be designed to prevent cross-contamination during NHP production. This includes implementing physical separations in production areas and using dedicated equipment for allergenic or sensitive materials. Improved air filtration and proper building ventilation systems help reduce the risk of airborne contaminants.
Clear handling procedures for raw materials ensure that there is no risk of cross-contamination throughout the production process.
Ensure Proper Labelling and Packaging
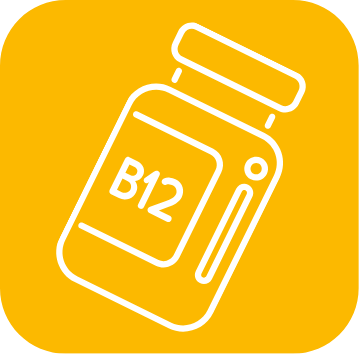
Accurate labelling and tamper-evident packaging are crucial for NHP GMP compliance. Labels must include clear dosage instructions, health warnings, and expiry dates, while packaging protects the product’s integrity.
Manufacturers are required to retain electronic records of labelling and packaging for at least one year beyond the product’s expiry date to ensure traceability and compliance.
Implementing a Quality Management System (QMS)
A well-structured Quality Management System (QMS) is essential for NHP manufacturers, packagers, labellers, importers, and distributors to maintain high-quality standards while adhering to the regulatory requirements set forth by Health Canada. The QMS ensures that every aspect of the manufacturing process is controlled, monitored, and documented to meet good manufacturing practices (GMP) standards.
Document Control Procedures: Document control is a cornerstone of any effective QMS. It ensures that all stakeholders have access to accurate, current information, which promotes consistency and supports regulatory compliance audits. Standard Operating Procedures (SOPs) are critical to define and standardize processes necessary to comply with GMP. For example, keeping batch records current allows for traceability, early detection of potential issues, and quick resolution in case of problems.
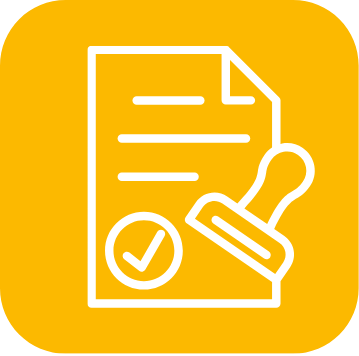
Change Control Management: A change control process ensures that any modifications to processes, materials, or equipment are systematically evaluated to determine their impact on product safety, quality, and NHP GMP compliance. Changes, such as introducing new ingredients, must be assessed, documented, and approved before execution. This structured approach helps maintain product integrity and prevents disruptions in the manufacturing process.
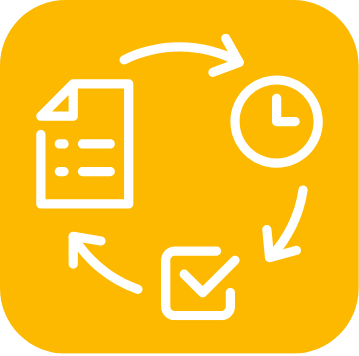
Deviation Handling and Corrective and Preventive Actions (CAPA): Deviations from established procedures must be addressed promptly. The Qualified Person for Quality Assurance (QAP) is responsible for evaluating the severity of deviations and determining their potential impact on product safety and quality. The CAPA process identifies the root causes of issues and implements actions to prevent recurrence. For example, if repeated equipment failures occur, new maintenance protocols may be introduced to address and prevent future deviations.
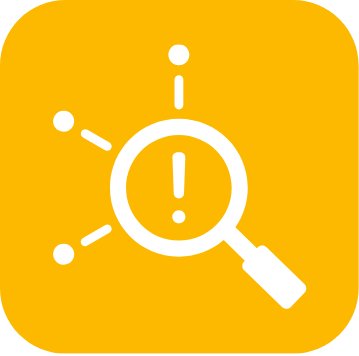
Risk Assessment and Mitigation: Effective quality risk management is a key component of a QMS. It involves identifying and mitigating risks that may impact product quality at every stage of the product lifecycle. Tools like Failure Mode and Effects Analysis (FMEA) are used to identify potential vulnerabilities before they escalate into significant issues. By proactively addressing risks, manufacturers ensure that products remain safe, effective, and compliant with the new GMP guidelines set by Health Canada.
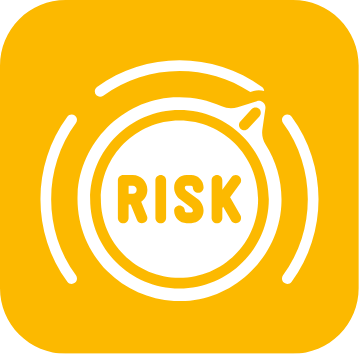
Final Remarks
Following GMP guidelines is not just a regulatory requirement but a fundamental practice that ensures the quality, safety, and consistency of Natural Health Products (NHPs). By implementing structured quality management systems, maintaining effective hygiene protocols, and rigorously validating manufacturing processes, companies can meet Health Canada’s standards while safeguarding public health. These practices not only help businesses maintain compliance but also build consumer confidence and long-term success in the competitive NHP market. Ultimately, a commitment to GMP is key to producing reliable, high-quality products that meet both regulatory and consumer expectations.
Ready to Elevate Your Product Quality?
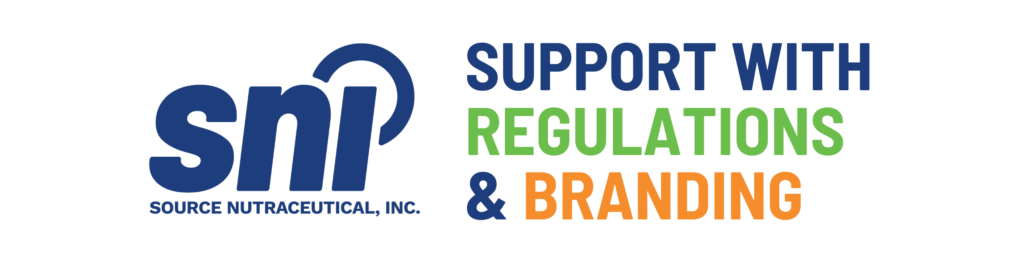
At SNI, we’re committed to helping you meet the highest standards of GMP compliance, ensuring your Natural Health Products are not only safe but consistently top-tier. Whether you’re just starting or looking to optimize your current processes, our expert team is here to guide you every step of the way. Let’s make sure your products stand out for their quality, integrity, and compliance. Reach out today and see how we can help you exceed industry standards and build trust with your consumers!
💡 Book a discovery call today to streamline the process and succeed in the Canadian market!
📩 info@sourcenutra.com
FAQ
What are GMP for NHPs?
GMP stands for Good Manufacturing Practices. These are rules set by Health Canada to make sure that natural health products, like vitamins or herbal supplements, are made safely and consistently. GMPs cover everything from the raw ingredients used, to how the final product is packaged, ensuring that each product is safe, effective, and of high quality.
Who makes sure NHPs follow GMP?
The responsibility for following GMP rules falls on the manufacturers, packagers, importers, and distributors of natural health products. To help with this, a Quality Assurance Person (QAP) must be in charge at each site to make sure the products meet the required standards.
What does a Quality Assurance Person (QAP) do?
A QAP is the person in charge of checking that products are made according to safety and quality rules. They ensure that everything is done correctly, from the production process to the final product, and take action if something goes wrong.
What happens if a company doesn’t follow GMP rules?
If a company doesn’t follow the GMP rules, Health Canada can take action, such as pulling products off the shelves or imposing fines. This is done to make sure that the public only has access to safe and properly made products.
How can companies stay up to date on GMP changes?
Companies need to regularly check updates from Health Canada and attend training programs on GMP. Being part of industry groups and subscribing to updates helps businesses stay informed about any changes in the rules.