Quality assurance (QA) plays a central role in the safety and credibility of natural health products (NHPs) in Canada. Manufacturers are required to meet high standards set by Health Canada to ensure their products are safe, effective, and made with consistent quality before they reach the consumer.
Canada’s regulatory framework for NHPs is among the most robust in the world. It holds companies accountable not just for the final product, but for every step in the production process, including sourcing, formulation, manufacturing, packaging, and labelling. This regulatory oversight ensures that NHPs are not only legally compliant but also safe and trustworthy for public use.
In this article, we explore what QA means for the NHP industry in Canada, what the key elements of a strong QA program are, and why it is essential for companies to make quality a core part of their operations.
What are Natural Health Products?
Natural health products are regulated under the Natural Health Products Regulations, which fall within the Food and Drugs Act. These products are used to maintain or improve health and are often intended to relieve minor ailments such as colds, digestive discomfort, or mild insomnia.
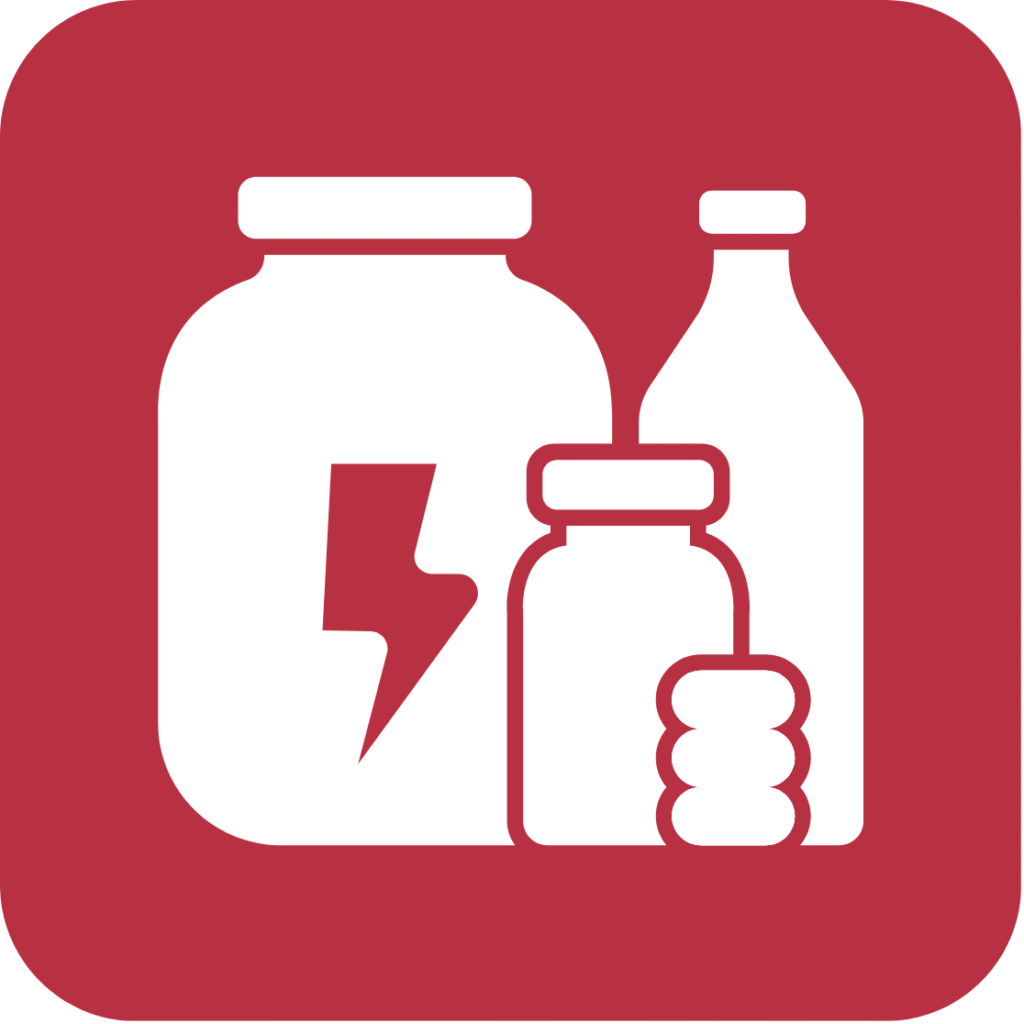
Health Canada defines NHPs as including:
- Amino acids, essential fatty acids, and probiotics
- Vitamins and minerals
- Herbal remedies
- Homeopathic medicines
- Traditional medicines (such as Traditional Chinese Medicine or Ayurveda)
Unlike prescription drugs, NHPs can be sold over the counter. However, they must receive Health Canada’s approval before entering the market. Approved products are assigned a Natural Product Number (NPN) or a DIN-HM for homeopathic products. This number signifies that the product’s safety, efficacy, and quality have been reviewed and authorized for sale in Canada.
The Importance of Quality in NHPs
Quality assurance in natural health products is directly linked to consumer safety. Products that are poorly manufactured may be contaminated, improperly labeled, or inaccurately dosed. These flaws can lead to health issues, including allergic reactions or interactions with other medications.
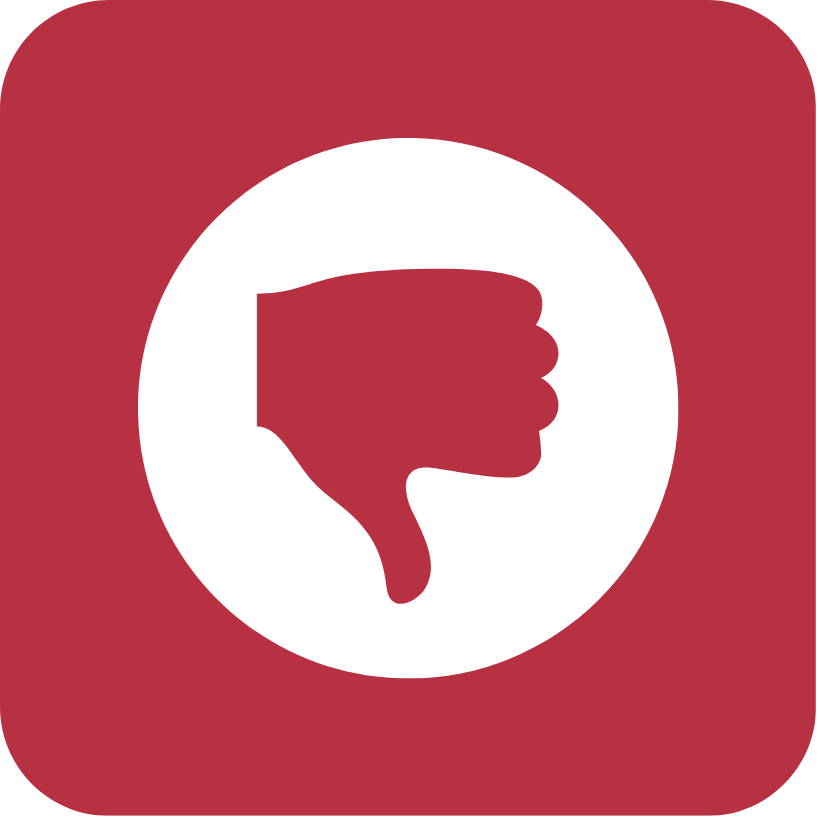
Poor-quality products also damage consumer trust. Inconsistent or ineffective products can erode confidence in a brand or even the broader category of NHPs. On the other hand, companies that prioritize quality are more likely to earn customer loyalty and avoid regulatory issues or costly recalls.
Compliance with Good Manufacturing Practices (GMPs) is one way to ensure this level of quality. GMPs are required by Health Canada and provide a structured framework for managing risks, verifying product consistency, and maintaining high standards throughout the production cycle.
Who Must Comply with GMP?
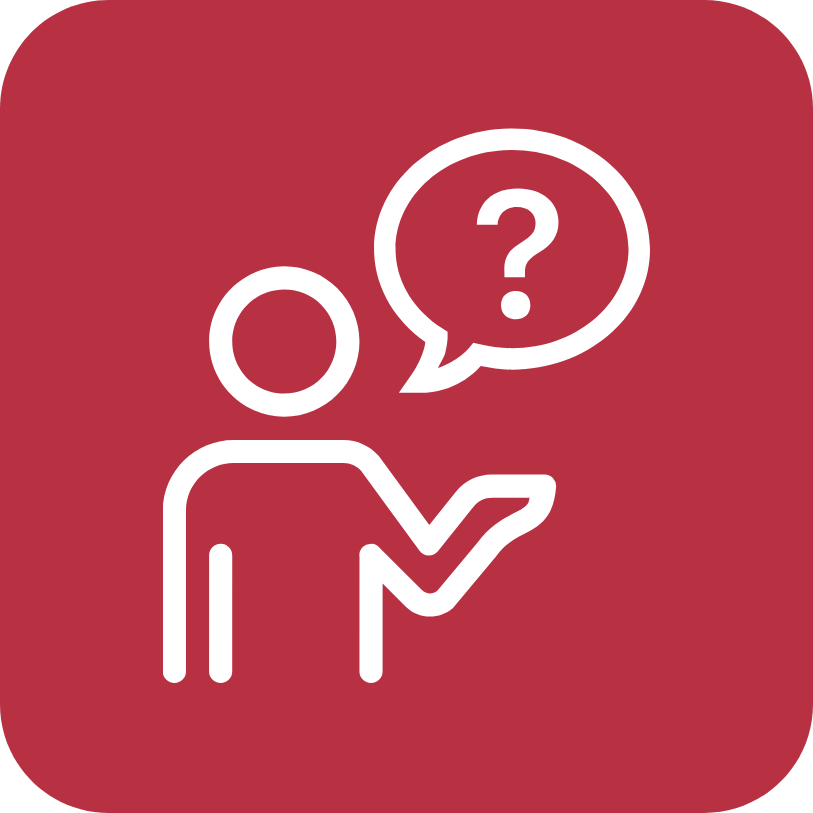
Every company that manufactures, packages, labels, or imports NHPs into Canada must follow GMP requirements. This includes businesses of all sizes. Whether a company is producing large-scale supplements or small batches of traditional herbal tinctures, it must maintain full control over its operations and meet regulatory standards.
Compliance means:
- Facilities must be clean, organized, and well maintained.
- Staff must be trained and competent in their roles.
- Manufacturing procedures must be documented and consistently followed.
- Every batch of product must be tested and verified before release.
Non-compliance can result in regulatory action from Health Canada, including license suspensions, product recalls, fines, or legal proceedings. Even beyond legal consequences, failing to comply can permanently damage a company’s reputation.
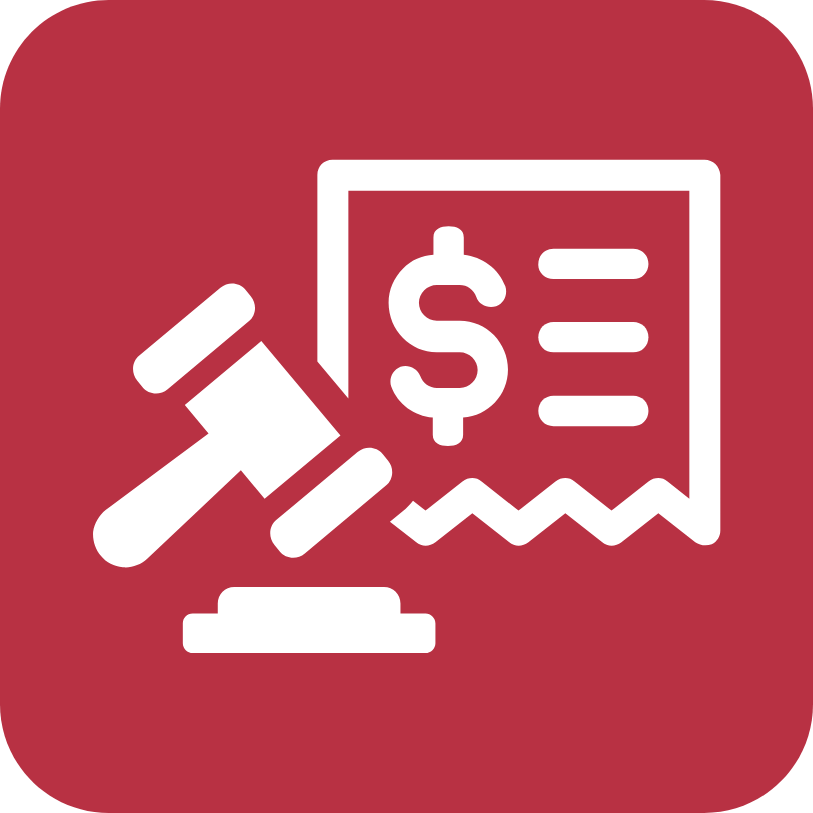
Good Manufacturing Practices as the Foundation of NHP Safety
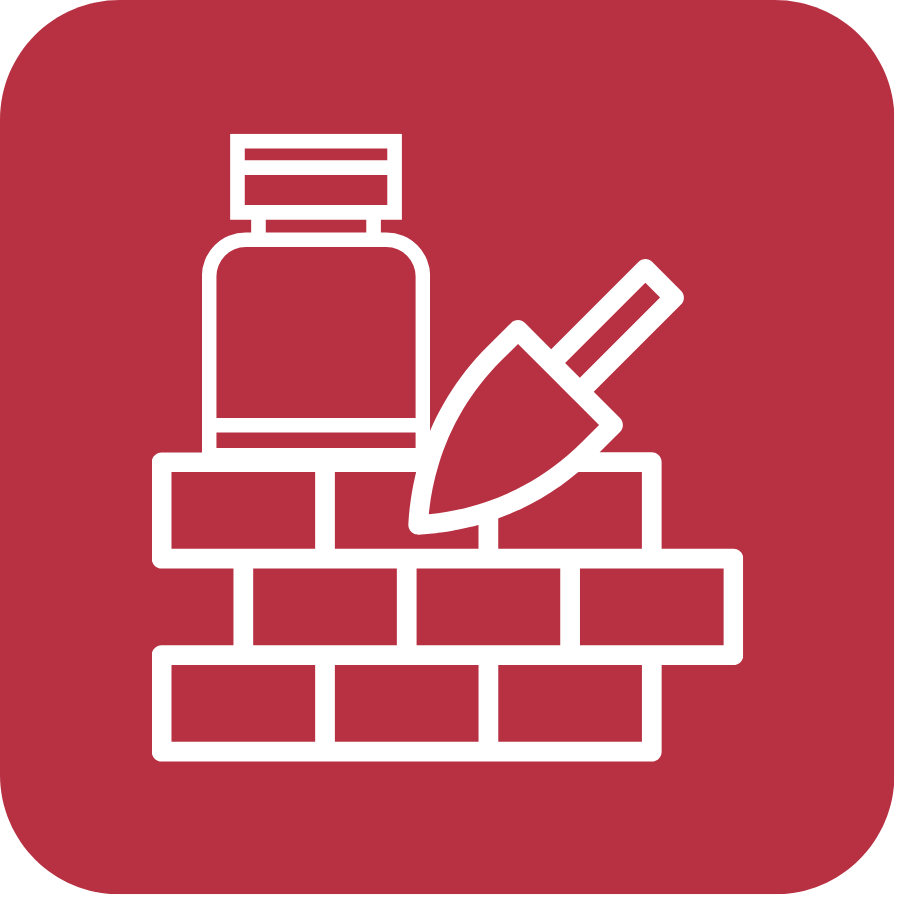
Good Manufacturing Practices (GMP) go beyond meeting regulatory requirements. They provide a structured framework to ensure the safe, consistent, and high-quality production of natural health products (NHPs).
GMP applies to every stage of the product lifecycle, beginning with the sourcing of raw materials and continuing through to the distribution of finished products. Adherence to these standards helps manufacturers prevent issues such as cross-contamination, dosage inaccuracies, and labeling errors.
By implementing GMP effectively, companies can manage quality risks, protect consumer health, and maintain a reliable supply of products that meet high standards.
Understanding Good Manufacturing Practice
In Canada, GMP for NHPs is defined in Part 3 of the Natural Health Products Regulations. It is enforced by the Natural and Non-prescription Health Products Directorate (NNHPD), a branch of Health Canada.
GMP covers the following key areas:
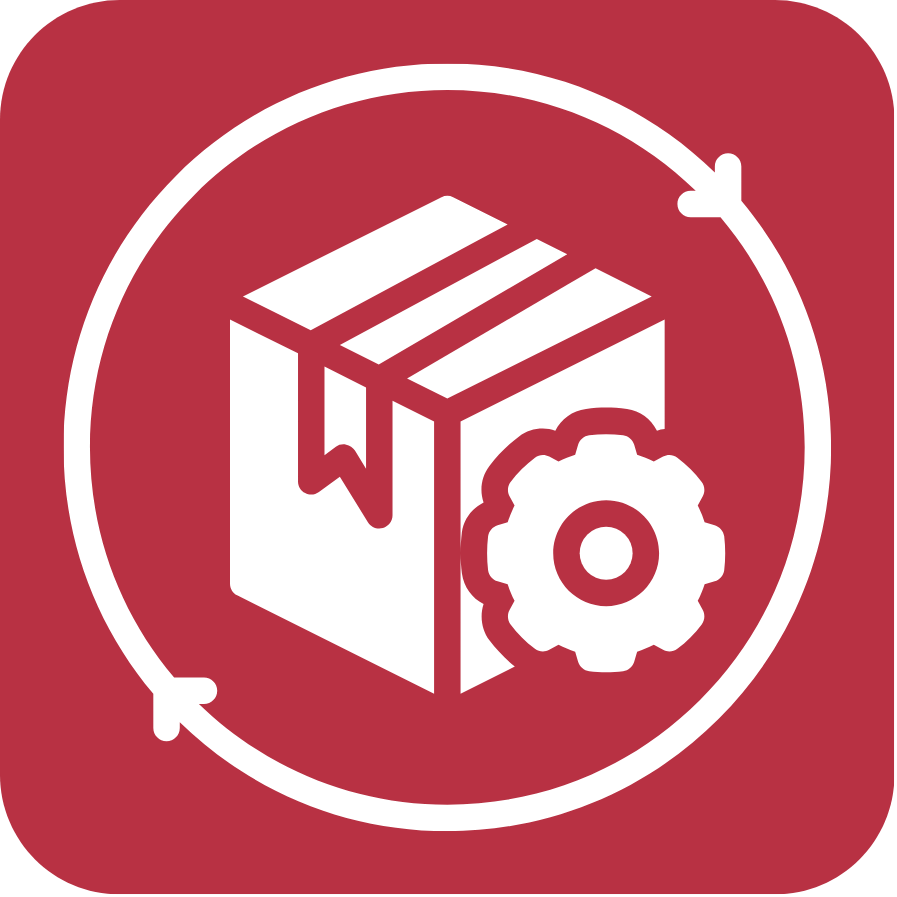
- Raw material verification: Every ingredient must be tested for identity, purity, and potency before use.
- Controlled manufacturing processes: Procedures must be clearly defined, documented, and followed to ensure consistent production.
- Finished product testing: Products must be tested to confirm they meet the established specifications for strength, safety, and stability.
- Record-keeping: Detailed records must be maintained at every stage to support traceability and accountability.
- Staff training: All employees involved in production must be trained and competent in GMP principles and procedures.
These elements work together to create a system that is proactive rather than reactive. When applied properly, GMP allows manufacturers to identify and solve problems early, before they impact consumers or the market.
The Four Pillars of GMP
To simplify GMP, it can be helpful to think in terms of four core pillars: People, Processes, Products, and Procedures.
People are at the heart of GMP. Staff must be properly trained and supervised, with a clear understanding of their responsibilities. Ongoing training ensures that employees remain current with industry standards and regulatory expectations.
Processes are the systems that guide how a product is made, packaged, and tested. These must be validated to ensure they consistently produce the desired result. Effective processes reduce the chance of error and help maintain compliance.
Products must meet the specifications set out during the product development phase. This includes the right dosage, correct labeling, and consistent quality. Testing must be performed on each batch to verify these criteria.
Procedures document how everything is done. They act as the blueprint for staff to follow and are essential during inspections or internal audits. Proper documentation helps demonstrate control and transparency.
The Non-Negotiable Nature of GMP
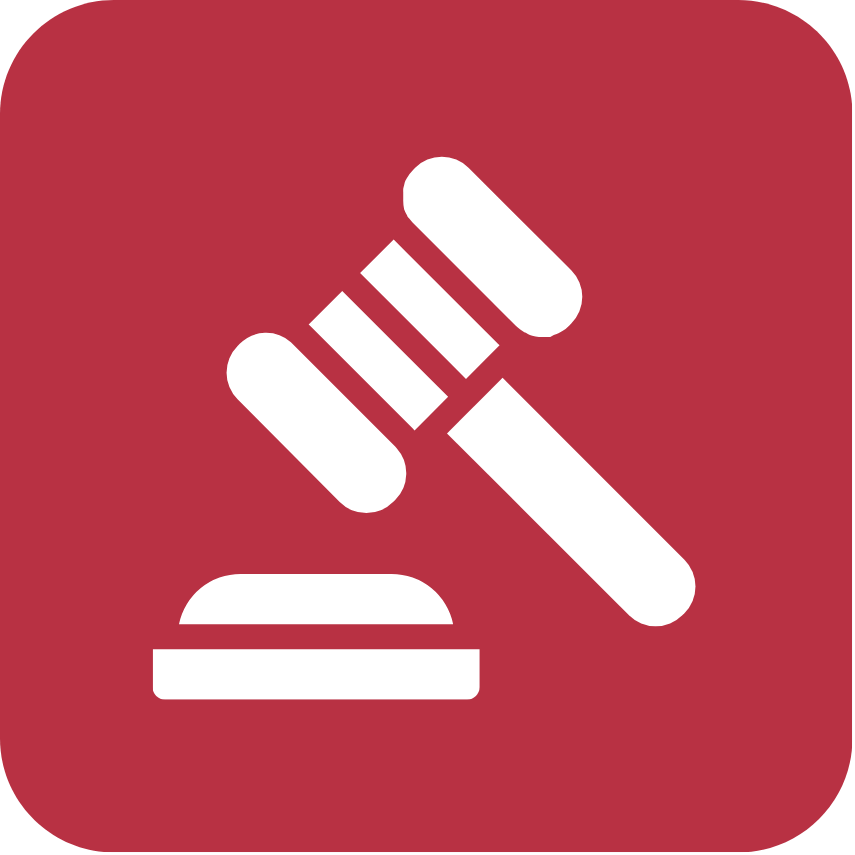
Good Manufacturing Practices (GMP) are a legal requirement in Canada and serve as an important foundation for quality and consistency in the natural health product sector. These standards help companies ensure that their products are made safely and meet regulatory expectations.
Meeting GMP requirements also supports future business opportunities. Many international markets recognize or require GMP certification for imported health products, so maintaining compliant practices in Canada can help facilitate access to those regions.
Adopting GMP reflects a company’s commitment to quality, safety, and professional standards. It also contributes to building consumer confidence and supporting long-term growth in the health and wellness industry.
How to Build a GMP-Compliant Quality System
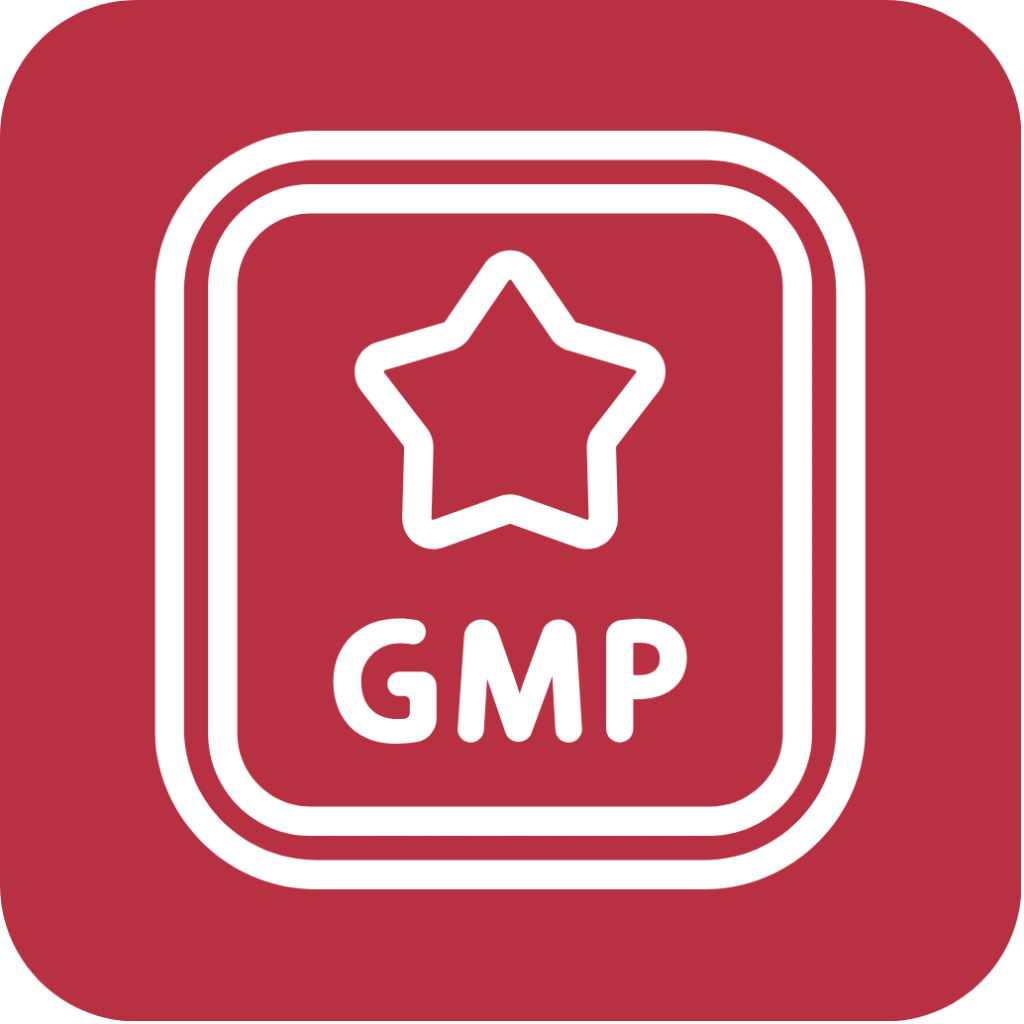
A successful GMP system starts with leadership. Management must make quality a priority by assigning responsibility to qualified individuals and providing the resources needed to maintain high standards.
Key steps include:
- Developing and maintaining Standard Operating Procedures (SOPs) for all critical activities.
- Training staff regularly and thoroughly on current GMP practices.
- Conducting internal audits to identify and correct weaknesses before inspections occur.
- Creating a culture of continuous improvement by reviewing performance metrics and feedback regularly.
These actions help build a stable, consistent, and compliant operation where risks are managed and product integrity is preserved.
Core Quality Assurance Elements in NHP Manufacturing
Quality assurance is about more than quality control testing. It is a comprehensive approach that addresses all aspects of production and post-market oversight.
Defining Product Specifications
Each NHP must have specifications that clearly define its identity, purity, quantity, and potency. These specifications are reviewed and approved by a designated Quality Assurance Person (QAP). No batch can be released for sale until it meets all requirements. These standards provide a benchmark for product consistency and safety.
Managing Sanitation and Hygiene
Clean production environments are essential. A well-developed sanitation program must include scheduled cleaning of equipment and facilities, staff hygiene protocols, and routine environmental monitoring. These measures reduce the risk of contamination and contribute to safe manufacturing practices.
Ensuring QA Oversight
The QA team plays a critical role in overseeing operations. Their responsibilities include reviewing production records, investigating deviations, approving batch releases, and ensuring that training and documentation are current. Their oversight is essential for maintaining control and addressing any issues that arise.
Maintaining Process Control
Consistency depends on reliable, validated processes. Manufacturing, packaging, and labeling must all follow established procedures. Changes to any process must be evaluated carefully, and any deviations must be documented and addressed promptly to avoid compromising product quality.
Keeping Accurate Records
Documentation is key to proving compliance. According to Sections 53 to 58 of the NHPR, manufacturers must keep detailed records of:
- Ingredient sourcing and testing
- Manufacturing and packaging processes
- Quality control tests
- Sanitation activities
- Complaint handling and recalls
These records support traceability and are essential during inspections or audits.
Quality Assurance Builds Consumer Confidence
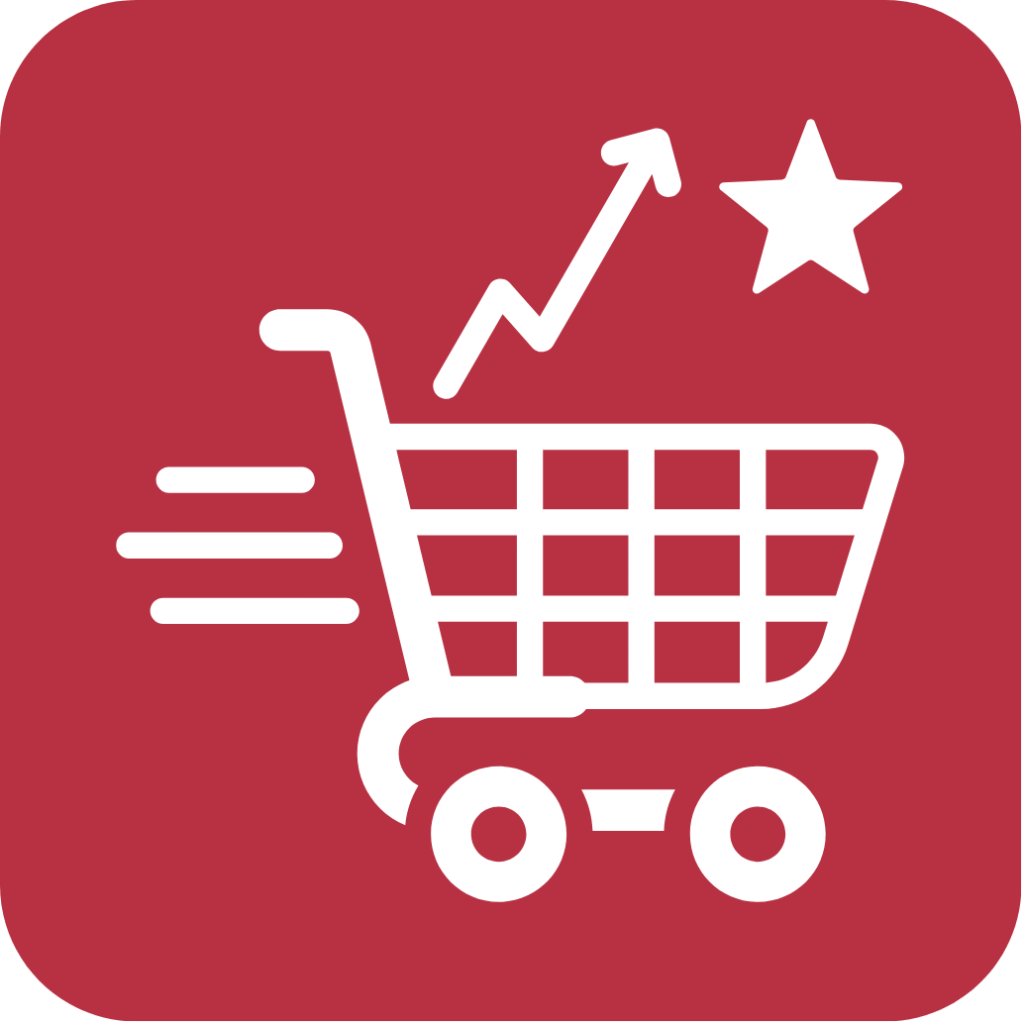
Consumers are becoming more informed and selective about the health products they buy. Brands that prioritize quality assurance send a clear message that they care about product integrity and consumer wellbeing.
Transparency in sourcing, clear labeling, and third-party testing are all signs of a quality-focused company. By communicating these efforts to consumers, companies can build trust, earn loyalty, and stand out in a competitive market.
Final Remarks
Quality assurance is not just a regulatory requirement for NHPs in Canada. It is a critical part of business success. A strong QA system protects consumers, satisfies regulators, and strengthens brand reputation.
With evolving technologies and growing consumer expectations, companies that invest in robust QA practices are better positioned for long-term growth. By building quality into every stage of production, they can deliver safe, consistent, and trustworthy products—every time.
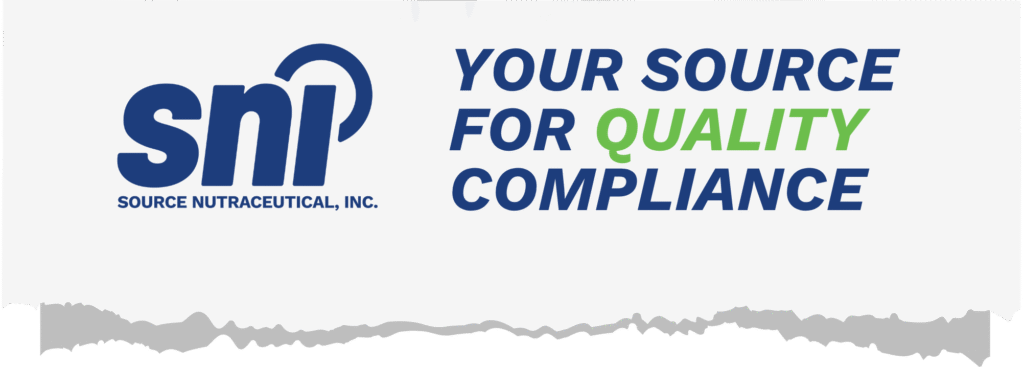
Whether your team requires assistance with Quality Assurance processes or you’re seeking a qualified third party to act as your designated Quality Assurance Person (QAP), SNI offers reliable and compliant solutions tailored to your needs.
At SNI, we recognize the critical role Quality Assurance plays in meeting Canadian regulatory standards. We also understand that for many businesses, building in-house QA capabilities can be time-consuming and resource-intensive. That’s where we come in.
Our team provides end-to-end support to ensure your products meet all necessary testing and compliance requirements before import—helping you avoid costly delays, held shipments, or regulatory surprises.
Complete the form below to learn more about our QA services and discover how we can help you streamline compliance while saving time and resources.
FAQs
What is a Natural Product Number (NPN), and why is it required?
A Natural Product Number, or NPN, is a unique identifier assigned by Health Canada to approved natural health products. It shows that the product has been reviewed for safety, effectiveness, and quality. Every natural health product must have an NPN or a DIN-HM for homeopathic medicines in order to be legally sold in Canada.
What are Good Manufacturing Practices (GMP) for natural health products in Canada?
Good Manufacturing Practices, often called GMP, are standards set by Health Canada to ensure natural health products are produced in a consistent and safe manner. They cover every part of the production process, including how ingredients are sourced, how products are made, and how they are packaged and labelled. The goal is to reduce risks such as contamination, mislabelling, and incorrect dosages.
Who is responsible for making sure natural health products meet GMP standards?
Any company involved in making, packaging, labelling, or importing natural health products in Canada must follow GMP requirements. Each business must have a qualified Quality Assurance Person who oversees the process and ensures that all products meet the required standards before they are released for sale.
What happens if a company does not follow GMP requirements?
Companies that fail to meet GMP requirements can face legal consequences. Health Canada may suspend licences, require product recalls, issue warning letters, or take legal action. In addition to these regulatory steps, failing to meet standards can also harm a company’s reputation and lead to a loss of consumer trust.
How can a company ensure its natural health products meet Canadian quality standards?
To meet Canadian quality standards, companies should establish a strong quality assurance program. This includes creating clear procedures, providing regular training for staff, keeping detailed records, and testing each product batch before it is sold. These actions help ensure product consistency and protect consumer safety.